Precision Turned Parts
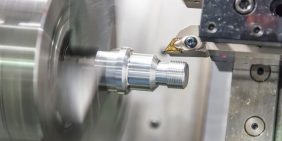
Below you can find answers to our customers’ most frequently asked questions regarding our precision CNC turned parts and components production processes and capabilities.
Our turning capabilities range from 0.5mm to 65mm in diameter from bar, and up to 300mm for billet work.
Tight turned parts tolerances of 5 microns can be achieved for high precision components. For mid-range parts, tolerances of +/- 0.01mm are generally achieved.
The smallest parts we turn are 0.5mm in diameter. We can also produce parts with sharp conical points, angles greater than 10 degrees and walls thinner than 0.5mm. We recommend you contact us to discuss your design first.
Yes, we have extensive knowledge of the materials we use and can recommend the best milling materials or turning materials for your application. These include stainless steel, plastic and brass turned parts.
Yes, plastic machining is possible with most rigid plastics, see our gallery for examples.
Yes, we can machine recessed text with a minimum stroke width of at least 0.5mm. For smaller text and more complex features, such as logos, we recommend laser etching.
Yes, material certificates are supplied with every delivery as standard. This is part of APT’s dedication to quality and the AS9100D standard and ISO 9001 accreditations we hold.
We hold the AS9100D standard, which is the global quality standard for the aerospace industry, and the ISO 9001 certification for quality management. These accreditations are fundamental to the way APT operates and demonstrate our ethos and commitment to quality control.
Our lead times range from 2 to 8 weeks, depending on the simplicity or complexity of your part. We will advise on the delivery timescale when we send your quotation.
Yes, thanks to our on-site storage and efficient production process, you can order in bulk and call off parts over a 12-month period. Placing a larger order also means you can also benefit from a better price.
Yes, we can extract design and engineering information from most manufactured components. Our services include producing technical drawings and 3D models using SolidWorks, if required.
Yes, with our Haas machining centres we offer prismatic machining to produce parts up to 700mm long.
For high quality CNC machined components, tolerances of 10 microns are possible. Mid-range tolerances of +/- 0.05mm are usually achieved.
We offer several different packing options, depending on the size and type of product. All our packaging is designed to provide effective protection against damage and ensure your orders are delivered in pristine condition.
We strive to keep our setup costs low and our setup times short. This means our minimum order value is just £350, plus materials. Any additional surface and heat treatment processes like plating, anodising and polishing are charged at extra cost.
Yes, we encourage customers to visit our premises. Please contact us to arrange a time as we can only accept visits by prior arrangement.